What are the factors that affect the lifespan of molds and wear parts used in a cement blocks making machine?
On March 11, 2024 by Javier James With 0 Comments
- Blogging
The lifespan of molds and wear parts used in a cement block making machine can be influenced by various factors:
- Material Quality: The quality of materials used in manufacturing molds and wear parts is crucial for their lifespan. High-quality materials with excellent wear resistance, hardness, and toughness, such as hardened steel or special alloys, can withstand the abrasive forces and stresses encountered during block production, leading to longer-lasting molds and wear parts.
- Design and Engineering: The design and engineering of molds and wear parts play a significant role in their longevity. Well-designed molds with proper reinforcement, optimized geometry, and effective cooling channels can withstand the rigors of block production and minimize wear and fatigue. Similarly, wear parts designed with adequate thickness, strength, and reinforcement can resist premature failure and extend their service life.
- Production Volume: The volume of blocks produced and the frequency of machine operation can impact the wear and tear experienced by molds and wear parts. High-volume production or continuous operation can accelerate wear and lead to faster deterioration of molds and wear parts compared to low-volume production or intermittent operation. Proper maintenance and replacement schedules should be implemented based on production volume to ensure optimal performance and longevity of molds and wear parts.
- Material Properties: The properties of the materials being processed, such as aggregates, cement, additives, and admixtures, can affect the wear characteristics of molds and wear parts. Abrasive materials, irregular particle shapes, or high-density aggregates can accelerate wear and increase the likelihood of damage to molds and wear parts. Adjusting the composition or properties of the raw materials may help mitigate wear and prolong the lifespan of molds and wear parts.
- Operating Conditions: The operating conditions of the block making machine, including factors such as temperature, humidity, vibration, and lubrication, can influence the wear rate of molds and wear parts. Extreme operating conditions, such as high temperatures or excessive vibration, can accelerate wear and fatigue, leading to premature failure of molds and wear parts. Proper maintenance, lubrication, and environmental controls are essential for minimizing wear and maximizing the lifespan of molds and wear parts.
- Maintenance Practices: Regular maintenance and proper care are essential for prolonging the lifespan of molds and wear parts. Routine inspection, cleaning, lubrication, and adjustment of molds and wear parts help prevent premature wear, corrosion, and damage. Timely replacement of worn or damaged components is crucial to avoid production downtime and ensure consistent block quality.
By considering these factors and implementing appropriate measures, manufacturers can maximize the lifespan of molds and wear parts used in cement block making machines, leading to improved productivity, efficiency, and cost-effectiveness.
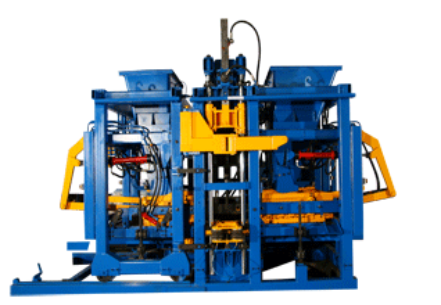
Comments are Disabled